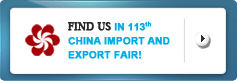
Solvent Extraction Process
Solvent Extraction Process means diffusion of solvent into oil-bearing cells of the raw material resulting in a solution of the oil in solvent. Just as the name suggests, solvent extraction refers to the process extracting oil from oil bearing materials by means of solvent, Various solvents can be used for extraction. However, after extensive research and consideration of various factors, such as commercial economics, edibility of the various products obtained from extraction, physical properties of the solvent especially its low boiling point etc. Hexane is considered to be the best and it is exclusively used in the solvent extraction process.
Solvent Extraction Process
- The prepared material from preparatory section is received in the feed hopper through rotary valve/plug conveyor. The material in the hopper and the rotary valve/plug conveyor together constitute an effective vapour seal while the latter also serves to regulate the feed. The hopper is further provided with the special switches for high level and low level indications. The latter if energized stops the band conveyor of extractor while the high level indication, transmits an audio visual signal to preparatory section for preparatory operator to take corrective measures.
- In the solvent extraction process, the extractor is long horizontal vessel, rectangular in cross section. An articulated band conveyor inside the extractor receives the material from feed hopper and transports it at a pre determined speed from the feed end to discharge end. The band conveyor moves over rails suitably located inside the Extractor and rides on specially constructed sprockets at either end. The speed of the band conveyor is easily adjustable within desired limits. An adjustable damper enables the regulation of height of bed of material on band conveyor.
- A series of sprayers located above the band conveyor enable perfect spray of the solvent on the moving bed. In the solvent extraction process, special spray breakers facilitate uniform distribution of solvent over the entire width of moving bed. Each spraying section is followed by a draining section.Fresh solvent is admitted into the Extractor near the discharge end of the moving bed of material and the full miscella is recovered from the initial stage; thus ensuring the perfect counter current flow of material and the solvent. It is not merely a simple counter current flow. The miscella circulates in a closed circuit in each of the successive section by overflowing from each hopper of the Extractor after increasing gradually its oil content in each hopper. The cleaning of the band conveyors is accomplished by high pressure jet spray of fresh solvent onto the return of band conveyor at discharge end which ensures perfect cleaning of mesh and eliminates completely the possibilities of choking of mesh and channeling.
Solvent Extraction Plants Workshop
In a nutshell, the solvent extraction process consists of treating the raw material with hexane and recovering the oil by distillation of the resulting solution of oil in hexane called miscella. Evaporation and condensation from the distillation of miscella recovers the hexane absorbed in the material. The hexane thus recovered is reused for extraction. The low boiling point of hexane (67°C / 152°F) and the high solubility of oils and fats in it are the properties exploited in the solvent extraction plant.